This case study supports and illustrates the theoretic factsheet "Quality control for HWTS manufacturing" with practical insights.
People living in slums and rural areas of India lack access to safe water and are unaware of basic personal hygiene practices. With the onset of the yearly monsoons, drinking water gets even more polluted. Under such conditions, incidence of waterborne diseases increases with negative impacts on life, health, productivity, and economic conditions of the already poor people. To improve these conditions among people living at the base of the economic pyramid (BoP) in India, Technology and Action for rural Advancement (TARA) a social enterprise and part of the Development Alternatives Group, based in Delhi, India, began to address these needs by producing and selling Aqua+, a 50 ml bottle of sodium hypochlorite solution (liquid chlorine). One bottle of Aqua+ has the ability to purify 500 litres of water, thus bringing down the cost of purification of 10 litres of water to INR 0.8 (USD 0.01).
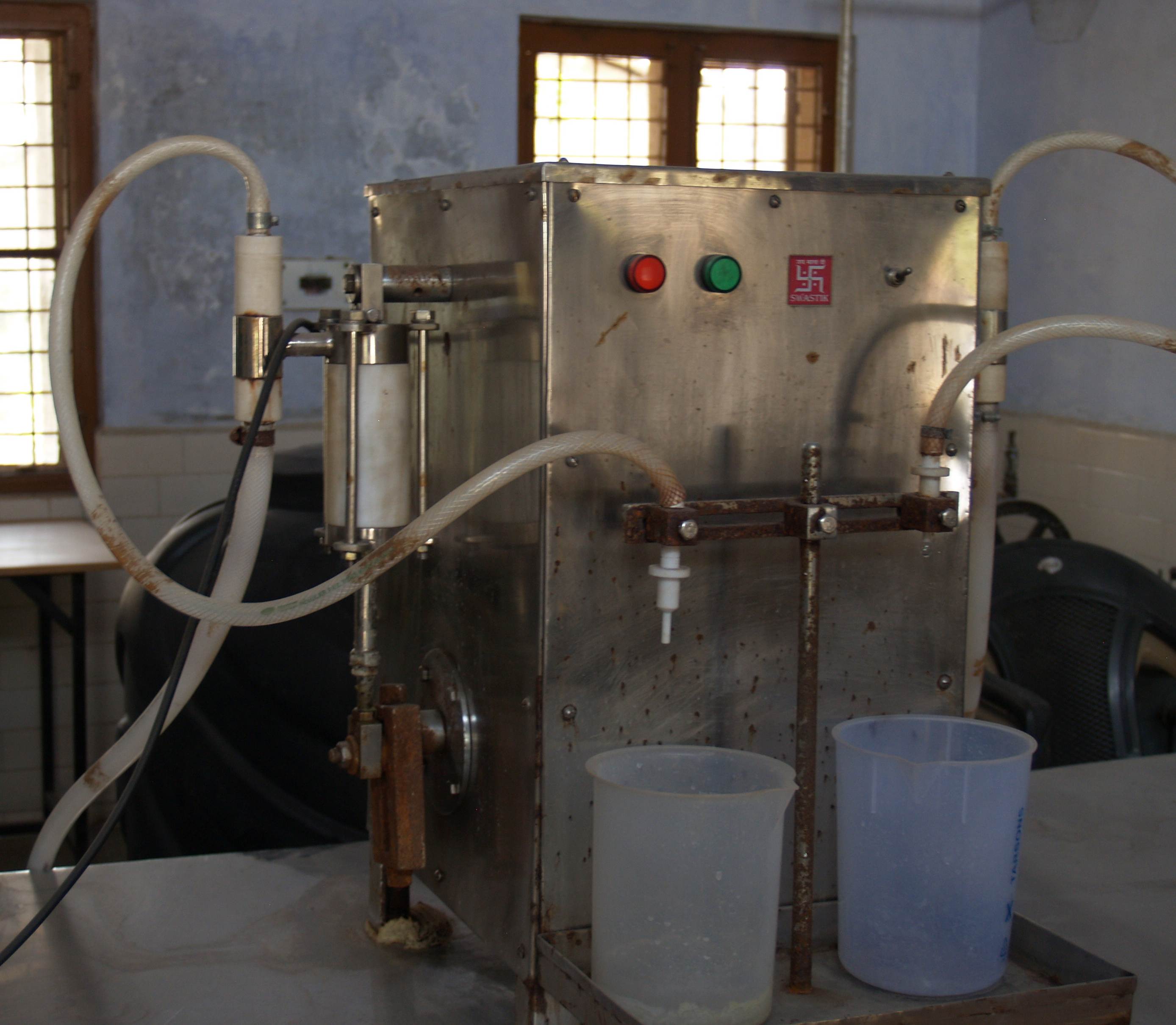
For these activities TARA has launched the social enterprise TARAlife Sustainability Solutions Pvt. Ltd (hereafter TARAlife) in 2013 to handle the production and sales of Aqua+ production unit in Orchha, Madhya Pradesh, India. With the set-up of the production and the commercialisation of Aqua+ TARAlife realised soon, that there is a need for consistent quality assurance to convince people, entrepreneurs and the government of its quality product. To meet these needs, TARAlife set up a thorough Quality Assurance and Quality Control protocol and implemented it in its centralised production unit – on top of this, TARAlife complies also with the ISO 9001:2008 standard for quality management.
The developed protocol addresses the following aspects:
- Quality Control – controlling the preparation, analysis and packaging of Aqua+ through sampling to check if production delivers accurate and precise results.
To implement quality control of production and packaging of Aqua+, several quality standards have been set such as how the bottle needs to be filled, labelled and packed. Accordingly a checklist for packaging has been developed. To control the quality of the sodium hypochlorite a concentration benchmark of 6 g/l has been set. Each batch of production is tested via titration measuring whether the benchmark has been exceeded or not.
- Standard Operating Procedure (SOP) - a written document for each analytical test and production step performed in the laboratory.
The SOP has been put in place through a detailed step-by-step documentation of the entire production process and quality control mechanisms to standardise the production procedure and quality control.
- Quality Assurance – to assure accuracy of the quality control as such, the procedures used during sampling and analysis need verification, including the review of the results, to determine if the developed procedures are adequate. To pursue the quality assurance correctly, a checklist has been developed that is used by the staff for every batch of production, to validate the achieved results.
For efficient implementation of the developed quality control procedures, the production staff was trained on all procedures and aspects of quality control as well as how to carry out the quality control and use the checklists and templates correctly.
- To implement a thorough quality control and assurance scheme it is pertinent to invest time in training responsible managers and executing staff. To keep a steady quality and improve the standardised procedures, it is highly recommended to monitor the processes continuously to assure its correct execution allowing to guarantee a high-quality product.
- The initially invested resources for developing standardised procedures will pay back over time as quality can be assured leading to an improved customer satisfaction.
- Providing customers with a certified product (like ISO certification) increases trust in the quality and efficiency of the product.
- Include quality control mechanisms from the beginning of your production, as it will enable you to measure your product’s quality steadily against set criteria that need to be met. Such measures allow you to improve your production on an ongoing basis.
- In order to figure out the different needs of external certification and quality compliance procedures it is very important to start investigating the different needs as early as possible by identifying the right public institution that is responsible for evaluating and issuing certifications. Keep in mind that these procedures might take months and should already be in place before production starts.
- Quality control mechanisms will reflect a reliable product and allow you to assure continuous quality. Including this measure in your marketing and communication work can support the increase of your customer base.