This case study supports and illustrates the theoretic factsheet "Production facilities - planning an efficient production process and layout of a factory" with practical insights.
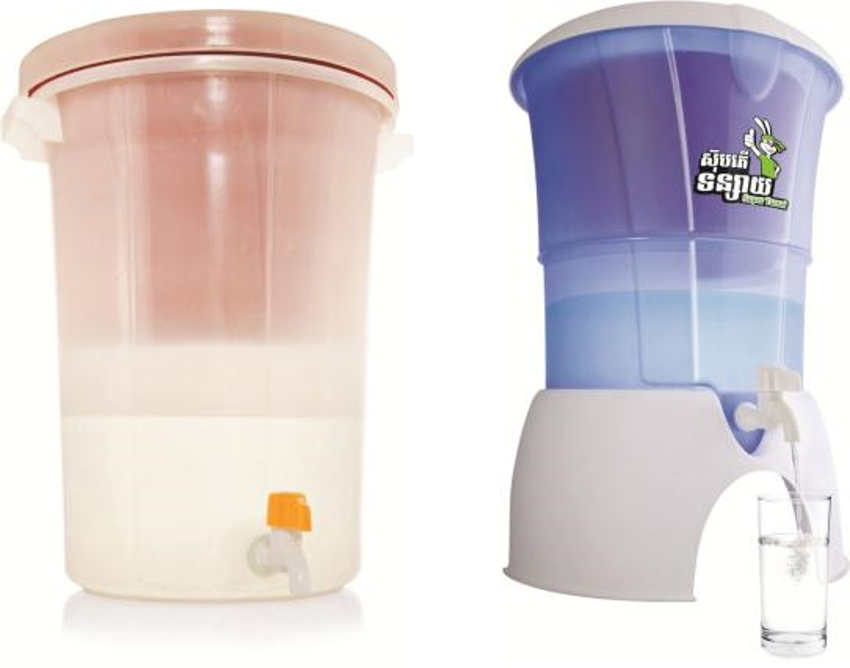
Source: Hydrologic, 2016
iDE is a global effort that spans offices in 14 countries, encompassing 4 social enterprises, employing nearly 1,000 people directly, and indirectly enabling many more through a market-based approach in agriculture, water, sanitation, and hygiene, and finance. iDE has started its ceramic filter project in 2001 with the introduction of the locally produced Tunsai ceramic filter (see image below). Due to social marketing activities and conviction of people to treat their water, the Tunsai performed well in the market and customers were highly satisfied with it.
The first factory was set up with seed funding from USAID in close collaboration with Potters for Peace for the factory implementation. During this early project stage, the locally trained ceramic filter producers had the capacity of producing 300 ceramic filters per month at iDE’s factory. As demand increased steadily, a new factory was built in 2010 with a more logical production flow and enough equipment and space to produce on average 5,000 pots per month. If production is pushed, peak production can reach up to 7,000 filters per month.
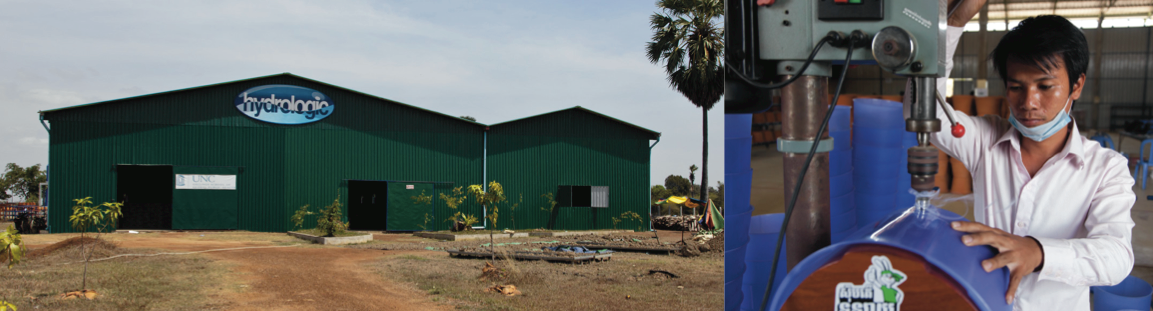
The initial production layout was inspired by the experiences of Potters for Peace in setting up ceramic water filter productions in Nicaragua. With a growing production over time some bottlenecks in the layout hampering the production flow were identified. These experiences led Hydrologic to change the layout of its new factory shown in picture above. Together with Australian manufacturing consultants, iDE staff developed the new layout with a logical process flow and space to expand the production over time. This development process also facilitated the definition of standardized operating procedures (SOP) and process set-up. To improve worker safety, dust and smoke suppression equipment and practices were introduced.
Today’s production process looks as follows:
Local clay is mixed with powdered rice husks, pressed into a pot shape, smoothed by hand, and baked in a kiln for 12 hours at 830°C. The rice husks burn away leaving microscopic pores that trap micro-organisms. The pots are coated with silver nitrate, a bactericide that provides a second barrier against bacteria. After the local production, the ceramic parts are assembled with the plastic parts either for the Tunsai or Super Tunsai filter. Each filter set is then packaged at the factory with a ceramic filter element, plastic receptacle and lid (different for each model), plastic spigot, plastic scrub brush, and graphic instructions.
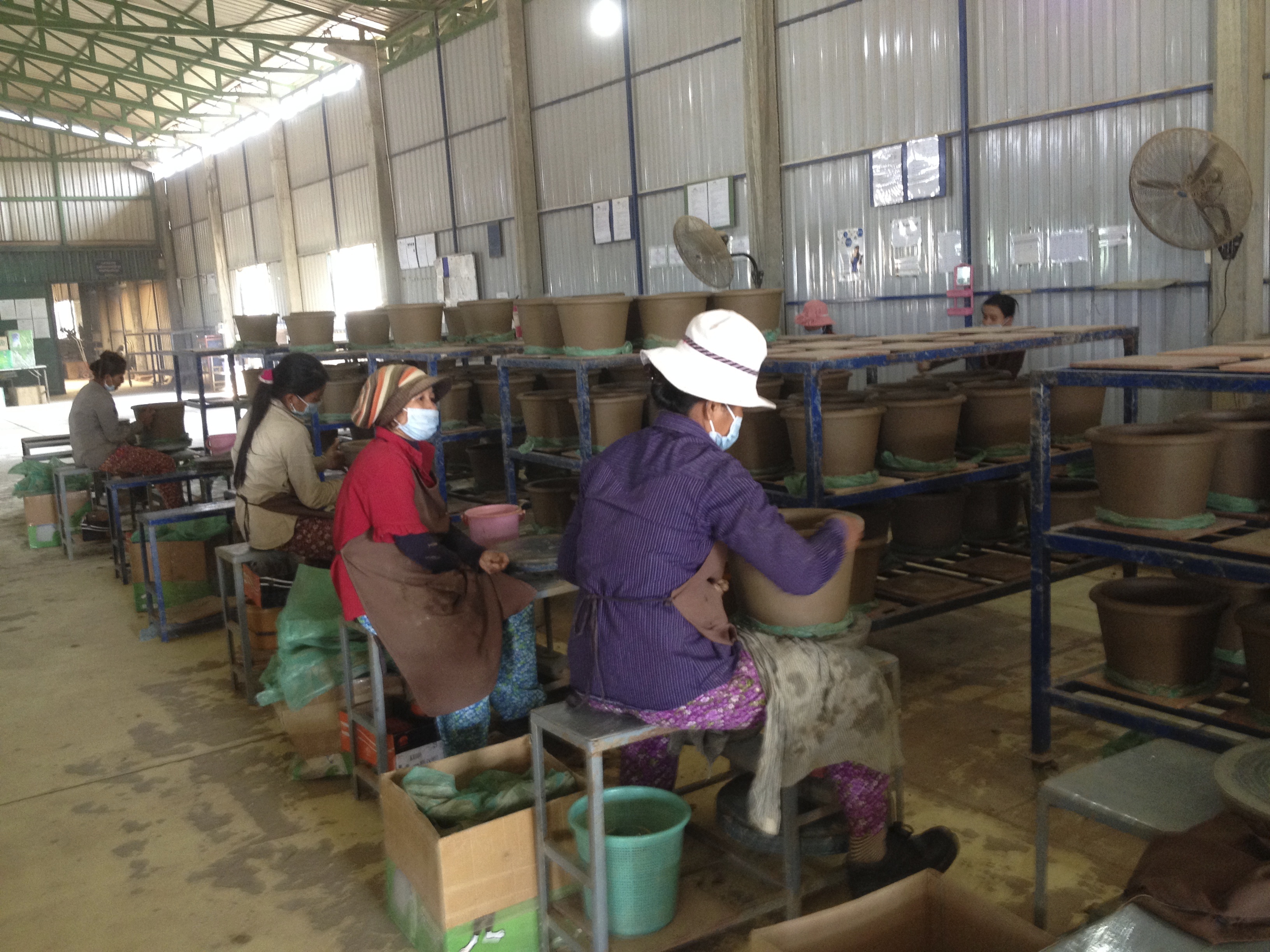
Hydrologic is registered with the Ministry of Commerce and undergoes annual inspection of the production facility and product manufacture by the Ministry of Industry and Handicraft. There is no specific product registration or certification in Cambodia for household water treatment products. Because the water filters are a health-related product, the introduction of a thorough internal quality control mechanism was of the utmost importance. To assure meeting the WHO water quality standards, Hydrologic has developed an internal product quality assurance process and standards that have independently been verified by The Gold Standard Foundation as part of the carbon finance project. The quality control mechanisms include:
- On-site flow-rate testing (2-4.5 l/h).
- Visual inspection before and after baking.
- Pots are discarded if defect or flow rate is outside the acceptable range.
Water quality testing: Water samples are tested at an external laboratory:
- Every 3 months (bacterial removal effectiveness).
- Every 6 months (arsenic content).
So far, the lab tests have been positive. 100% bacterial removal and arsenic contaminants results far below the minimum set by the WHO.
Hydrologic has already developed a thorough business case, but ongoing improvements in terms of quality and production processes are key in order to keep the business viable and improve economies of scale.
Learn from others
The manufacturing process is constantly evolving as problems are identified and solved. This ongoing learning has been facilitated by experience shared with other filter manufacturers in Cambodia and around the world. For setting up a ceramic filter factory, there has extensive research been done by Potters for Peace making it available in various documents for practitioners, among it a manufacturing set-up manual.
Improve quality and reduce waste through standardization
An early challenge was to reduce the number of defective pots, which reached 30% of production in certain months, causing costs that hindered the company to break-even. This was addressed by ensuring more consistency in the manufacturing process by standardizing mix ratios and kneading time and modifying oven (kilns) for more uniform heat distribution. This led to reducing wastage rates, which are now consistently standing below 10%.
Quality of production and delivery
To ensure a high-quality product, especially important for HWTS in order to assure safe water at the point of use, high quality resources (access to raw materials, labour force, infrastructure, and transportation) have to be guaranteed on-site.
Capital is key for the infrastructure
Producing Tunsai filters is not very capital intensive as clay and rice husk are available at very low cost or even for free. The installation of a production site and the purchase of land is capital intense though. Especially the kiln to burn the clay pots can cost you up to USD 200,000 (in Cambodia). Summed up, Hydrologic is estimating capital needs at USD 500,000 (depending on the country context and availability of needed technology) to be able to set up a basic ceramic filter factory with a capacity of around 5,000 filters per month.
Keep improving your business model
For starting a safe water business you should have a clear vision on what you want to achieve and where you want to go. Based on these prerequisites develop a strong business model and keep innovating to meet the needs of the market.
Identify and invest in your human capital
Aiming at an efficient production requests not only to have a well-designed factory but most important the right people that produce and handle the different tasks. To set up a strong team you have to invest in Human Resources and identify the right people for manufacturing, finance, administration, sales and a visionary and capable management team. Capital for expansion is also the human capital within your company.